Understanding Die Casting Die Manufacturers and Their Impact on Metal Fabrication
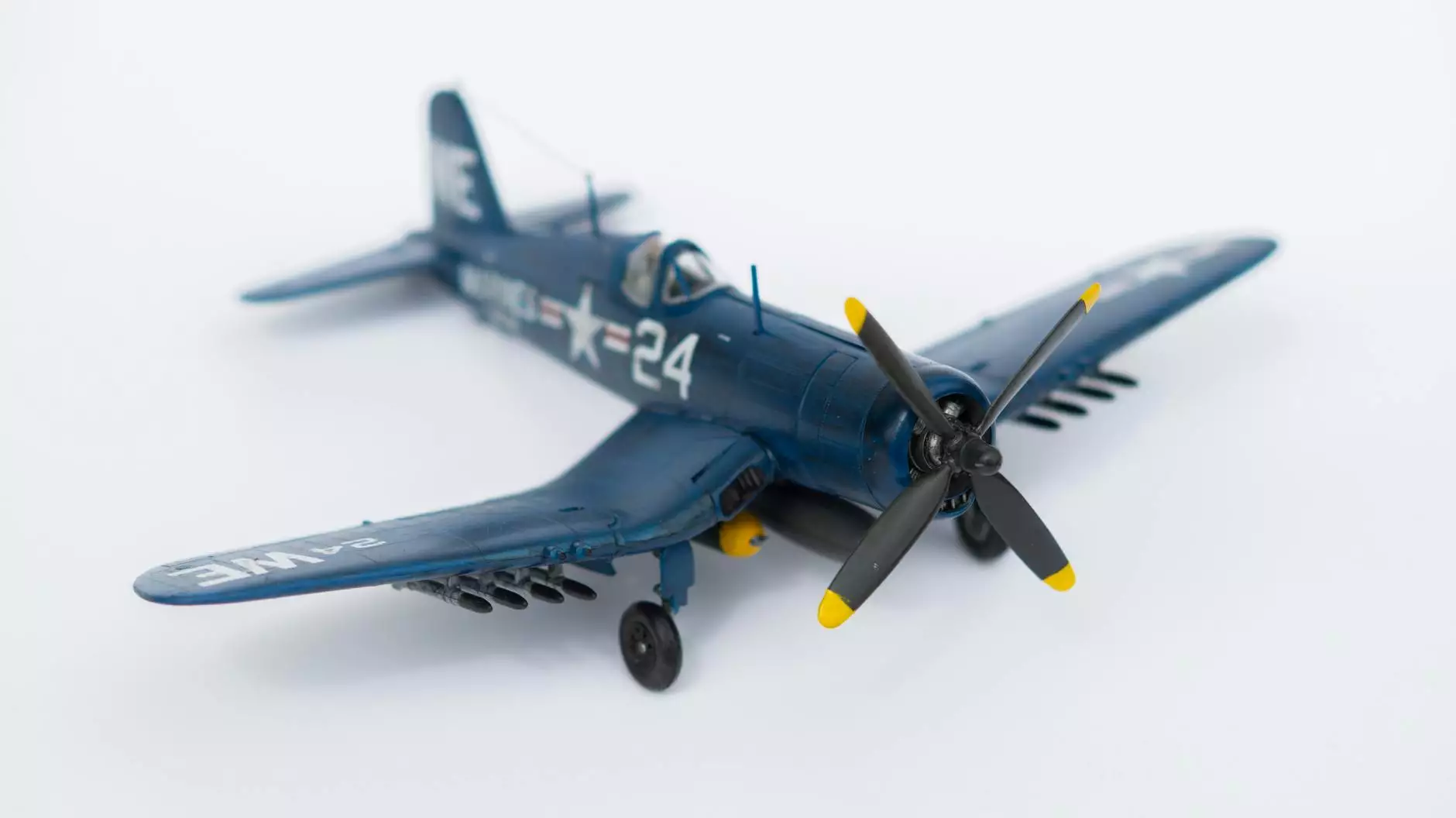
In the world of metal fabrication, the precision and efficiency of manufacturing processes are paramount. Among these processes, die casting has emerged as a pivotal technique, renowned for its ability to create intricate and durable metal components. At the heart of this process lie die casting die manufacturers, who provide the essential molds required for shaping metals into detailed and enduring products. This article delves into the intricate role of die casting die manufacturers, examining their processes, advantages, and their overarching impact on the metal fabrication industry.
The Essentials of Die Casting
Die casting is a manufacturing process characterized by high-pressure injection of molten metal into a mold. This method is favored for its capability to produce complex shapes with exceptional dimensional accuracy. Industries that often utilize die casting include automotive, aerospace, electronics, and consumer goods. The products that result from this process range from small components, such as gearbox housings, to larger structures like engine blocks.
The Role of Die Casting Die Manufacturers
At the core of die casting lies the die itself, a precision-engineered tool crafted by die casting die manufacturers. These manufacturers specialize in designing and fabricating molds that allow for the efficient production of various metal parts. Their expertise is crucial in ensuring that the molds provide not only the desired shape but also the dimensional accuracy required for each component.
Types of Die Casting Processes
Die casting can be categorized into two main types: hot chamber die casting and cold chamber die casting. Understanding these processes is essential for recognizing how die casting die manufacturers tailor their products to meet industry demands.
1. Hot Chamber Die Casting
In hot chamber die casting, the molten metal is injected into the die from a chamber that is heated to maintain the metal in liquid form. This method is typically used for zinc, magnesium, and some alloys of lead due to their lower melting points. Hot chamber die casting is known for its speed and efficiency, allowing for high-volume production runs.
2. Cold Chamber Die Casting
Conversely, cold chamber die casting involves pouring the molten metal into a chamber separate from the die. This method is often used for metals with higher melting points, such as aluminum and copper. Cold chamber techniques are typically slower than hot chamber techniques but can produce stronger and more structurally sound components.
Benefits of Using Die Casting
The benefits of die casting extend beyond the mere production of metal parts. Here are some compelling advantages:
- High Precision: Die casting produces highly accurate components with minimal tolerances.
- Complex Geometries: Manufacturers can create intricate shapes that would be difficult to achieve with other methods.
- Surface Finishing: The surface of die cast products typically requires minimal finishing work, saving time and costs.
- Material Efficiency: The die-casting process utilizes a limited amount of metal, which reduces waste significantly.
- Scalability: The process is ideal for high-volume production needs, with fast cycle times.
The Importance of Choosing the Right Die Casting Die Manufacturer
When considering die casting die manufacturers, it is crucial to evaluate their capability in meeting specific project needs. Here are several factors to consider:
1. Experience and Expertise
A manufacturer’s experience in the industry can significantly influence the quality of the dies produced. Established manufacturers who have worked with various industries understand the distinct requirements of different applications.
2. Technology and Equipment
The technology used in die manufacturing plays a crucial role in the precision and quality of the final product. Modern die casting die manufacturers should employ advanced machinery and software for design and manufacturing processes to ensure consistent results.
3. Material Selection
Different projects require different materials, and die casting die manufacturers should offer a range of options. Whether the project demands aluminum, zinc, or magnesium, the right manufacturer should have the capabilities to work with these materials effectively.
4. Customer Support and Service
Effective communication and support throughout the project can ensure the success of the collaboration. Manufacturers should be open to discussions about design adjustments, timelines, and project logistics.
Quality Assurance in Die Casting
Quality assurance is an integral part of the die casting process. Die casting die manufacturers must adhere to strict standards to ensure that the molds they produce will result in high-quality components. This includes:
- Design Validation: Ensuring that the die design meets the specifications of the final product.
- Material Testing: Using quality materials in the die to withstand repeated use without failure.
- Dimensional Verification: Regular checks during production to confirm that parts maintain required specifications.
- Surface Quality Control: Ensuring that the finish of die-cast parts meets aesthetic and functional standards.
Environmental Considerations in Die Casting
As industries become more conscious of their environmental impact, die casting is evolving to include sustainable practices. Die casting die manufacturers are increasingly adopting eco-friendly approaches, such as:
- Recycling Metal: Utilizing recycled materials in the die casting process reduces waste and promotes sustainability.
- Energy Efficiency: Implementing energy-efficient machinery and practices to minimize energy consumption.
- Waste Management: Developing methods to reduce or eliminate waste produced during manufacturing.
Future Trends in Die Casting
The die casting industry is continually evolving with advancements in technology and changes in consumer demand. Here are some trends that die casting die manufacturers are likely to embrace in the future:
1. Automation and Robotics
With the rise of automation, more manufacturers are integrating robotic systems into their production lines. This not only increases production efficiency but also enhances precision and consistency in die casting.
2. 3D Printing for Die Manufacturing
3D printing is becoming a valuable tool in the creation of die casting dies, allowing for rapid prototyping and complex geometries that are difficult to achieve with traditional methods.
3. Advancements in Materials
Ongoing research into new materials could lead to stronger, lighter, and more durable die cast products, broadening the scope of applications across different industries.
Conclusion
The role of die casting die manufacturers in the metal fabrication industry cannot be overstated. Through their expertise, advanced techniques, and commitment to quality, they create the molds that make high-quality, complex metal parts possible. As the demand for precision and efficiency in manufacturing grows, these manufacturers will continue to be at the forefront of innovation, paving the way for more sustainable and advanced production processes.
For businesses looking to explore the benefits of die casting, choosing a reliable die casting die manufacturer like Deep Mould at deepmould.net can lead to lasting partnerships that drive success in their respective industries. The future of die casting is bright, and with the right manufacturers, the possibilities are endless.