The Ultimate Guide to Vacuum Forming Silicone Sheets
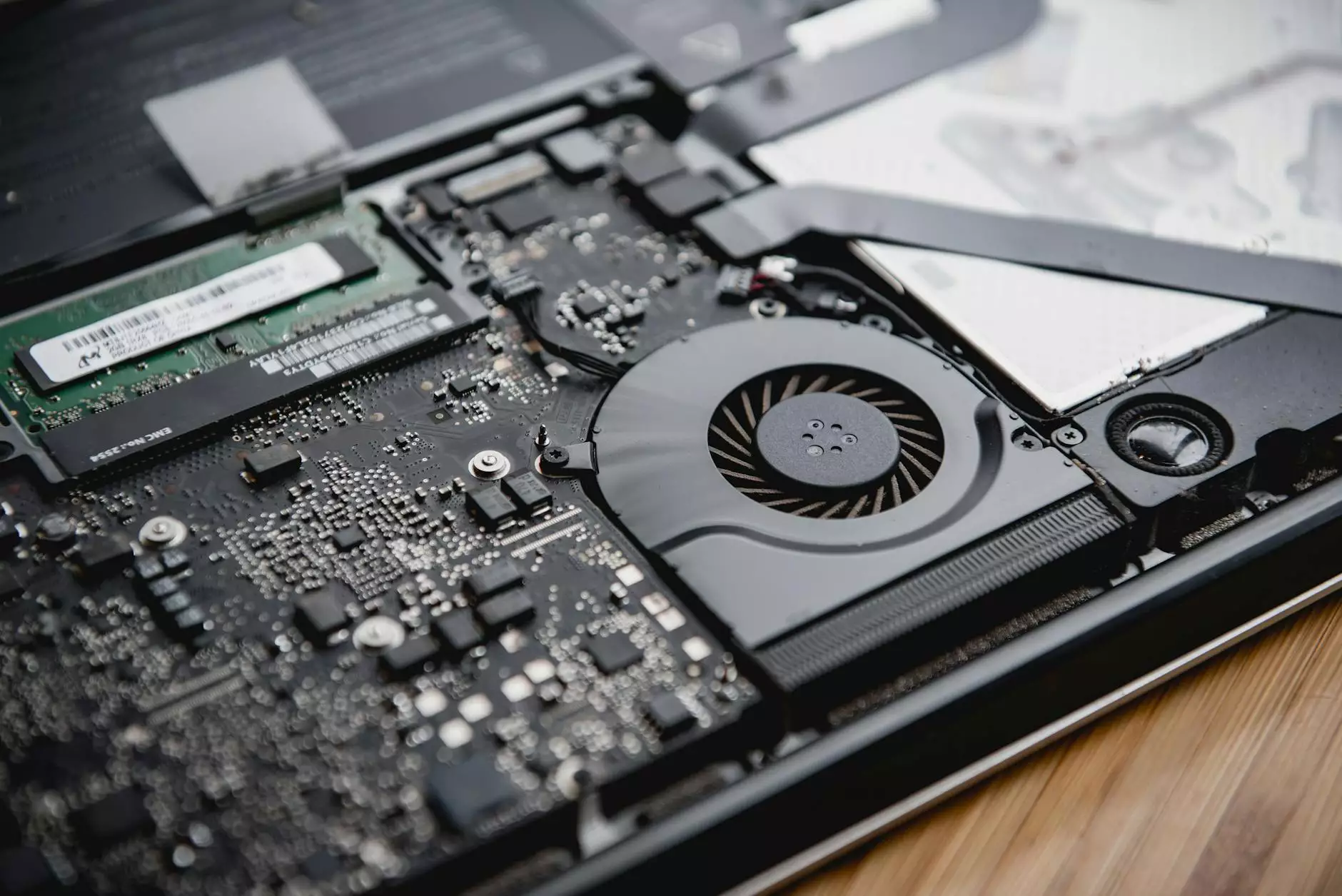
Vacuum forming silicone sheets have become an essential component in various industries, thanks to their unique properties and versatile applications. Whether you are in the automotive, healthcare, or product design sectors, understanding the nuances of vacuum forming silicone sheets can significantly enhance your manufacturing processes and product quality.
What is Vacuum Forming?
Vacuum forming is a manufacturing process where a sheet of plastic is heated until soft and then formed over a mold using a vacuum. This technique allows for the creation of complex shapes and is widely used in various industries.
Understanding Silicone Sheets
Silicone sheets are highly revered for their durability, flexibility, and resistance to heat and chemicals. When it comes to vacuum forming, using silicone sheets can provide several advantages over traditional materials. Let’s delve deeper into the characteristics that make vacuum forming silicone sheets stand out.
Characteristics of Silicone Sheets
- Heat Resistance: Silicone sheets can withstand high temperatures, making them ideal for applications that require heat stability.
- Flexibility: The inherent flexibility of silicone allows for intricate designs without the risk of cracking or breaking.
- Durability: Silicone is resistant to wear and tear, ensuring that the sheets have a long lifespan.
- Chemical Resistance: Silicone materials can endure exposure to various chemicals, adding to their versatility.
Benefits of Using Vacuum Forming Silicone Sheets
Incorporating vacuum forming silicone sheets into your production process can drive significant benefits:
1. Enhanced Design Freedom
When you utilize vacuum forming silicone sheets, the design possibilities are virtually unlimited. The materials can easily take on complex shapes and contours, allowing companies to innovate and create unique products. From automotive components to medical devices, the ability to mold silicone into precise forms enhances creativity and functionality.
2. Cost-Effectiveness
While high-quality silicone sheets can represent a higher upfront cost than other materials, their longevity and durability contribute to reduced production costs over time. The vacuum forming process minimizes material waste because the excess can often be reused, leading to more economical operations.
3. Quick Production Times
The vacuum forming process takes comparatively little time, allowing for rapid prototyping and production. This rapid turnaround is crucial in industries like healthcare and consumer electronics, where time to market can determine a product's success.
4. High-Quality Finish
Products made from vacuum forming silicone sheets often feature excellent surface finishes, allowing for aesthetic customization. This quality is especially beneficial for brands focused on delivering premium products.
Applications of Vacuum Forming Silicone Sheets
Silicone sheets used in vacuum forming have applications across several industries:
- Automotive: Engine covers, dashboard components, and seals.
- Healthcare: Surgical trays, medical device casings, and custom prosthetics.
- Electronics: Protective covers, casings for devices, and heat shields.
- Consumer Goods: Packaging, display stands, and molded product housings.
Choosing the Right Supplier for Your Silicone Sheets
Finding a reliable supplier for vacuum forming silicone sheets is crucial for maintaining quality standards and ensuring a smooth production process. Here are some tips:
1. Quality Assurance
Always inquire about the quality control processes in place. Reputable suppliers will conduct rigorous testing on their products to ensure they meet industry standards.
2. Product Range
A good supplier should offer a variety of silicone sheet options, including different thicknesses, colors, and types, such as natural rubber membranes and rubber membranes.
3. Technical Support
Choose a supplier that provides excellent customer service and technical support. This can be invaluable when you need assistance with product selection or troubleshooting during the vacuum forming process.
4. Competitive Pricing
While you should never compromise on quality, it is essential to find a supplier that offers competitive pricing. Requesting quotes from multiple suppliers can help you make an informed decision.
Maintenance and Care for Vacuum Forming Silicone Sheets
To prolong the life of your vacuum forming silicone sheets, proper maintenance is essential:
- Cleaning: Use mild soap and water to clean silicone sheets. Avoid abrasive materials that can damage the surface.
- Storage: Store silicone sheets flat and avoid exposure to direct sunlight or extreme temperatures to prevent warping.
- Inspection: Regularly inspect sheets for wear and tear, especially if they are used frequently in production.
Conclusion: The Future of Vacuum Forming with Silicone Sheets
The landscape of manufacturing is evolving, and vacuum forming silicone sheets are at the forefront of this change. With their unique advantages, these sheets provide innovative solutions for various sectors, enhancing productivity and quality. As industries continue to seek efficient methods of production, the versatility and resilience of silicone sheets will undoubtedly play a pivotal role in shaping the future of manufacturing.
For businesses looking to source high-quality vacuum forming silicone sheets, consider exploring the offerings at vacuum-presses.com. Their wide range of silicone and rubber membranes, vacuum system parts, and dedication to quality make them a leader in the industry.